日刊工業新聞にて、2014年4月〜6月、13回にわたって「実践TPS」と題してトヨタ生産方式を解説した記事を連載しました。これは、トヨタ生産方式の陥りやすい内容、注意すべき内容を、広い領域の中の点と点で、書き著したものです。少し専門的ですが、エッセンスを凝縮したものなので、トヨタ生産方式を勉強するための参考になるかと思います。(ここに記載の記事は、第一回目のものです。記事の著作権は著者に、版権は日刊工業新聞社にありますのでご注意ください)
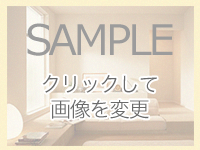
日刊工業新聞にて、2014年4月〜6月、13回にわたって「実践TPS」と題してトヨタ生産方式を解説した記事を連載しました。これは、トヨタ生産方式の陥りやすい内容、注意すべき内容を、広い領域の中の点と点で、書き著したものです。少し専門的ですが、エッセンスを凝縮したものなので、トヨタ生産方式を勉強するための参考になるかと思います。(ここに記載の記事は、第一回目のものです。記事の著作権は著者に、版権は日刊工業新聞社にありますのでご注意ください)
トヨタ生産方式コンサルタントとして、TPSの考え方に基づき活動してきて特に最近感じることがあります。それは、現場を見るとまだまだやるべきことがあるにもかかわらず、手がつけられていないことが多く、また工場での改善への推進力が弱まっているということです。商品競争力の問題とか、海外との競争とかの問題もあり、生産現場のコスト競争力が及ばなくなっているという議論があります。そのような環境はあるにしても、名だたるメーカーの製造工場を訪問しても、ひと目で改善点が見えるようなことがあります。気づいていないのか、やり方を知らないのか、放置しているのか、指導者のまずさなのか、理由はいくつも考えられます。
先に、「『見える化」』を実践をしようとする際、『何が正常で何が異常であるかを明確にする』という視点に立てばと思います」と書きました。バラエティー番組で、”見える”か?、”見えない”か?とやっていたのは、おもしろいですね。
「作業標準は、標準作業を行うため、・・・・・」などと言われても、最初は混乱しますね。この、作業標準と標準作業という言葉は、間に「の」を入れて理解するよう教えられました。「作業の標準」、「標準の作業」というわけです。後半の熟語が主体と考えます。
製造業において、また間接業務でも、「改善」という言葉は、KAIZENという英語で世界に通用する言葉であるといわれます。また日本では、改善でなく「カイゼン」だとする人も見えますし、さらには、「TPS=改善」と思えるような書き方をしている例もあります。 このように、人によって「改善」に寄せる思い・見方はたくさんあるようですが、英語圏の人に説明して一番すっきりとしているなと感じたのが、”continuous improvement" です。ちなみに、”continual” を使っていた例もみましたが、少しニュアンスが違うように思います。
製造でTPSといったらTOYOTA PRODUCTION SYSTEM とイコールのことだと認知されています。今でこそ、トヨタ自動車さんの広報資料等でもTPSと書かれています。しかしながら、ここにいたる歴史を考えてみるのも良いでしょう。大野耐一さんは、決してTPSなどという言葉を使っていないようです。丁寧に「トヨタ生産方式」と言い、「トヨタ生産方式の基本思想は『徹底したムダの排除』であり、しかも、それを貫く二本の柱がある。 (1)ジャスト・イン・タイム (2)自働化」という説明の仕方だ、 としています。 そもそも、生産雑誌の記事に於いて、「当N社では『生産システムはNPSと言う』」・・・・等と言っていたように思います。会社の名前分だけ略語が出てきていました。
トヨタ生産方式(TPS)のバイブル「トヨタ生産方式」(大野耐一著)が発行された時、新人で技術・開発部門にいましたが、当時の役員が全員に読むよう指示されました。因みに今見ると、発刊されて1ヶ月もたっていないのに、4版です。それ以来、また生産調査というTPSを推進する部門では特に一生懸命勉強し、いまだに勉強中の身です。最近、これは英語(英会話)を勉強するのと似ているなと思うようになりました。日本人は、話しかけられて、かなりの人が ”I can't speak English." と答えるので、英語を話せるじゃないかとまた言われます。
在庫は、我々がした事の結果なのです。我々がやっているしくみの結果が現れるのです。また、単に在庫水準だけを目標とするのではなく、強いモノづくり職場を追い求める姿勢が大切です。少し長いですが、書籍「セル生産」のコラムを以下に引用します。
コラム④ : 一生に一度の在庫低減
私たちは、「在庫管理」と言うと、すぐ「最大最小の管理レベルは」という話をします。これはこれできちんと管理できていればいいのですが、落とし穴があります。
まだ駆け出しのころ、在庫の指導を受けたことがあります。
「かんばん」という言葉は、ひらがなを使います。あまりこだわらなくても、本質を理解すれば良いのでしょうが、「トヨタ生産方式(看板方式)を導入し、極めました」と表現しているのを見たりすると、少し疑問に感じます。 歴史的に、ひらがなの理由は他にゆずるとして、トヨタ生産方式を真に理解することは難しいですね。大野耐一さんがジャスト・イン・タイムと自働化という2本柱でトヨタ生産方式を説明しているものの、考え方を理解することが大切だといわれます。また、会社の内容によって、レベルによって、やり方・方法が変わってきます。
生産性を追求する時、ややもすると「1日でどれだけ生産するか」という方向に行ってしまいがちです。そのことが如何に多いのかと先輩のコンサルタントが、よくお話されます。「つくり過ぎによる不良在庫のムダ」を発生させないことが真の生産性であり、大野耐一さんの目指す「ジャスト・イン・タイム」への挑戦でした。昨今、原因・理由はともあれ、結果として大きな商品在庫をかかえて苦しんだ車業界も在庫調整が一巡し少し明るさがみえてきたのは何よりです。
少し前からの本ですが、「関口真理ら:インドのことがマンガで3時間でわかる本」を読んで、新たに再認識できたこともあって、インドへの入門としてお勧めします。多くの方の手になるもので、経験に裏打ちされた良い内容だろうと思います。また、「3時間でわかる」の書名と「日頃、インドは簡単にわからないと話している」ことと矛盾していますと「はじめに」に書いて見えますが、どの国でも、自分の目で見て感じることが大切でしょうね。海外で仕事をすると、「人間は、どこでも変わりはない」という当たり前のことを実感しますね。
トヨタ生産方式は、常に進化していると言われます。トヨタ生産方式自主研究会(通称自主研)の中に身をおきましたが、ある時突然、「これは、常により良い造り方を追求する場なんだな」と頭に浮かんだことがあります。これらの一般に言われる改善活動を外から始めて見ると、単純に効率だけを追求しているように勘違いし抵抗を感じるのは、私も同じでした。特に、技術屋と呼ばれる人の抵抗は多いです。一つには、トヨタ生産方式を指導すると称する乱暴なコンサルタントをいまだに見聞きすることもあるからでしょう。
インドの製造業でも、日本の各種指導団体が以前より指導に行っており、改善活動の重要性は感じているようです。
特に、オーナー層は、競合していてもお互いにつながりがあったりして、またいろいろな他社も見学したりして、これらの活動の成果を認識し、工場の体質改善をしなくてはいけないと思っているようです。 ところが、トップの思いが下まで伝わっているかと言うと疑問を感じることがあります。
大野耐一さんは、著書「トヨタ生産方式」で現場主義の立場で「目で見る管理」の手段として「標準作業」を重要なものと位置づけています。また、トヨタ生産方式を研究したLIKERらは、 ”THE TOYOTA WAY FIELDBOOK"(日本版;ライカー他「ザ・トヨタウェイ 実践編」 の中で、
ひとに優しいモノづくり職場をつくるトヨタ生産方式コンサルトです
Toyota Production System(TPS/LEAN)
Consulthing Firm
■オンリーワンのモノづくり Only-one manufacturing
■モノづくりはひとづくり Making good use of personnel
■合理的な考え方のできる人材育成 Rational way
■ひとにやさしい職場づくり Considerate to workers
■継続的改善のできる風土づくり Continuous Improvement
Process Design Co., Ltd. Japan
6-1-2 Aoyagi-cho, Chikusa-ku,
Nagoya City, Aichi Prefecture 464-0852, JAPAN
Phone :(+81)(0)80-3645-0612
FAX : (+81)(0)52-732-5178
E-mail : mail@jitps.co.jp